TEMPERATURE MONITORING IN HYDROCARBON FEED CRACKERS
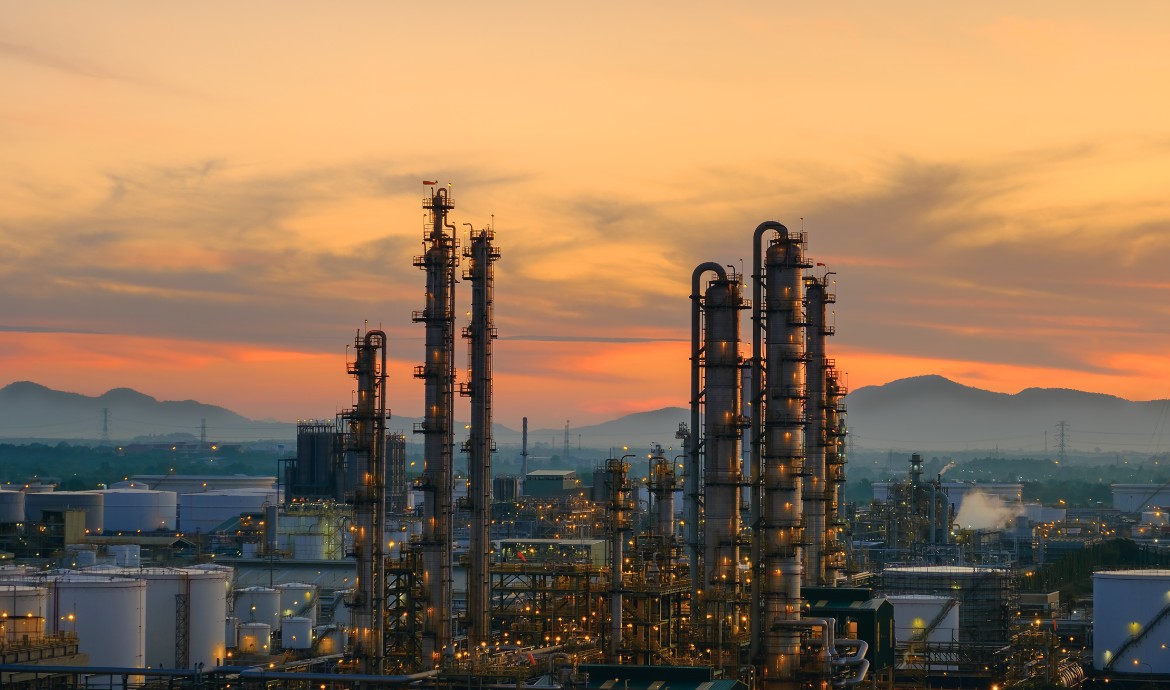
CATEGORY: Petrochemical Processing
PRODUCTS: Industrial Temperature Assemblies, Corrosion Resistance
DATE: November, 2021
Background
In the petrochemical industry, hydrocarbon feed crackers play a pivotal role in breaking down complex hydrocarbons into more straightforward, commercially valuable molecules like ethylene and propylene. The extreme conditions inside these crackers present a corrosive environment, which puts enormous strain on traditional temperature sensors. The inability of these sensors to withstand corrosive elements was leading to frequent failures, increased maintenance costs, operational inefficiencies, and jeopardised safety protocols. A robust, corrosion-resistant temperature monitoring solution was clearly needed.
SOLUTION
Addressing the corrosive environment within the hydrocarbon feed crackers, the plant engaged with our engineering team who are experts in corrosion-resistant sensor technologies. Instead of opting for an incremental upgrade, a radical approach was adopted to replace the conventional sensors with advanced, corrosion-resistant alternatives. These new sensors were constructed with materials specifically engineered to resist corrosive damage over an extended period, while also being designed to seamlessly integrate with the plant’s existing control systems.
Customised Services
The solutions provided were meticulously tailored to the plant's unique operational challenges. Regular consultations with on-site personnel were held to ensure that the new corrosion-resistant sensors aligned closely with operational needs and could be easily integrated into the existing infrastructure.
ENGINEERING EXCELLENCE
The new sensors represented a triumph of engineering over a particularly hostile environment. Utilising cutting-edge material science and simulation tools, the vendor was able to design sensors that not only met but exceeded the strict industry standards for corrosion resistance, reliability, and longevity.
RESULTS
The project yielded immediate and profound benefits:
- Extended Sensor Lifespan: The new sensors proved highly resilient against corrosion, drastically reducing the need for frequent replacements.
- Enhanced Operational Efficiency: Reliable temperature readings allowed for fine-tuned control of the cracking process, resulting in improved yield and quality.
Cost-Efficiency: The longer-lasting sensors led to significant savings in both parts and labour. - Safety and Regulatory Compliance: The dependable sensors ensured safer operating conditions and facilitated easier compliance with rigorous industry regulations.
In summary, the deployment of corrosion-resistant temperature sensors has had a transformative effect, elevating the plant’s operational excellence, safety protocols, and compliance standards