TEMPERATURE MONITORING IN CATALYST TANKS
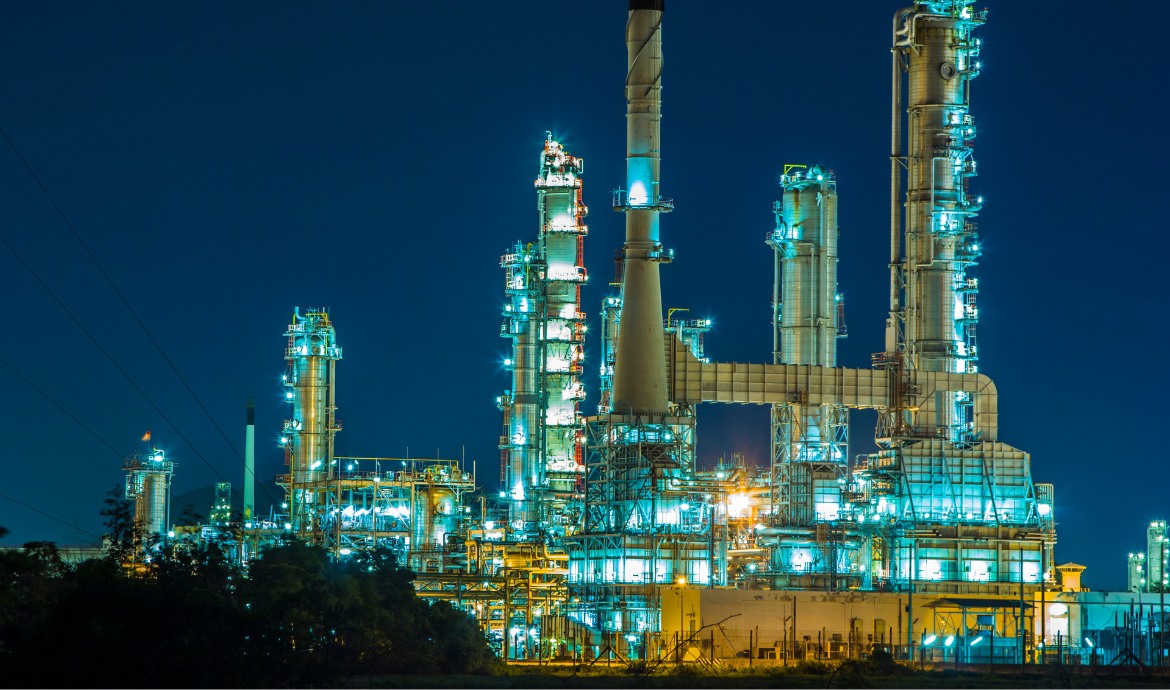
CATEGORY: Catalyst Processing
PRODUCTS: Multipoint Temperature Assemblies
DATE: January, 2021
Background
In the fast-paced world of catalyst processing, where reactions occur under precise conditions, maintaining uniform temperature within catalyst tanks is critical. Incorrect temperature measurements can lead to undesirable reactions, lower yields, and potentially hazardous conditions. For one facility, the challenges were particularly acute due to the limitations of their existing single-point thermocouples, which were unable to provide an accurate temperature profile of the entire tank. This lack of comprehensive temperature monitoring led to inefficiencies, safety risks, and compromised the quality of the output. As a result, a need arose for a more sophisticated and reliable temperature monitoring system, calling for a specialised solution that could address these challenges.
SOLUTION
Facing the complex challenges associated with inaccurate and insufficient temperature monitoring, the facility sought to overhaul its existing single-point thermocouple system. The limitations of the previous setup were that they provided temperature readings at only one location within the catalyst tank, leaving operators in the dark about potential temperature gradients and hotspots. This had consequential impacts on both safety and efficiency, with instances of uneven catalyst reactions and suboptimal usage of resources.
To address these concerns, the facility engaged Thermo Electric Instrumentation because of our proven track record in advanced multipoint temperature measuring solutions. After a comprehensive analysis, we recommended the installation of a multipoint thermocouple system, designed to provide temperature readings at several different points within the catalyst tank. The advantage of this setup was immediately clear: it would provide a full, three-dimensional temperature profile of the catalyst tank, thereby eliminating the blind spots that plagued the previous system.
Our engineering team took things a step further by customising the multipoint thermocouple assembly to fit the specific dimensions and operational requirements of the facility’s catalyst tank. This customisation process involved the use of advanced modelling software to simulate various configurations, ensuring optimal placement of the thermocouples to capture the most relevant data.
Another significant aspect of the solution was the inclusion of real-time data analytics and reporting features. This allowed plant operators to instantly receive temperature data and make real-time adjustments to the process variables, such as reactant flow rates and stirrer speeds, thereby achieving optimal reaction conditions.
Customised Services
From the initial consultation to the project's completion, a bespoke service approach was followed. The team engaged in extensive dialogues with the customer to fully grasp their specific issues and tailored the multipoint thermocouple solution to meet these unique challenges. Updates and adaptations were communicated transparently, ensuring that the solution remained aligned with the customer's operational objectives and timelines.
ENGINEERING EXCELLENCE
The multipoint thermocouple system was engineered to meet the highest standards of quality and reliability. Utilising cutting-edge technology and materials, our engineering team conducted in-depth analyses to ensure that the solution would meet all operational requirements. The multipoint thermocouples underwent rigorous testing to certify their durability and performance under various conditions, to ensure that they exceeded the client expectations.
RESULTS
The implementation of the multipoint thermocouples had a transformative impact on the facility’s operations, as noted by the following outcomes:
- Enhanced Temperature Monitoring: The new system allowed for far more accurate temperature monitoring across different sections of the catalyst tank.
- Increased Efficiency: The more accurate temperature readings enabled a more efficient use of catalysts, reducing waste and operational costs.
- Improved Safety: The enhanced monitoring capabilities of the new system reduced the risk of undesirable reactions, thereby enhancing workplace safety.
- Quality Control: More accurate temperature readings led to improved quality of the end products, thereby enhancing customer satisfaction and brand reputation.
- Compliance and Regulations: The improved monitoring and control brought the facility into better alignment with industrial safety standards and regulations.
- Cost Savings: By improving efficiency and reducing waste, the facility saw a significant reduction in operational costs, with a rapid ROI for the new system.
In summary, the introduction of multipoint thermocouples into the facility’s catalyst tanks not only improved operational efficiency but also significantly enhanced safety and compliance, positioning the plant for future growth and competitiveness.