HIGH PRESSURE COMPONENT SAFETY
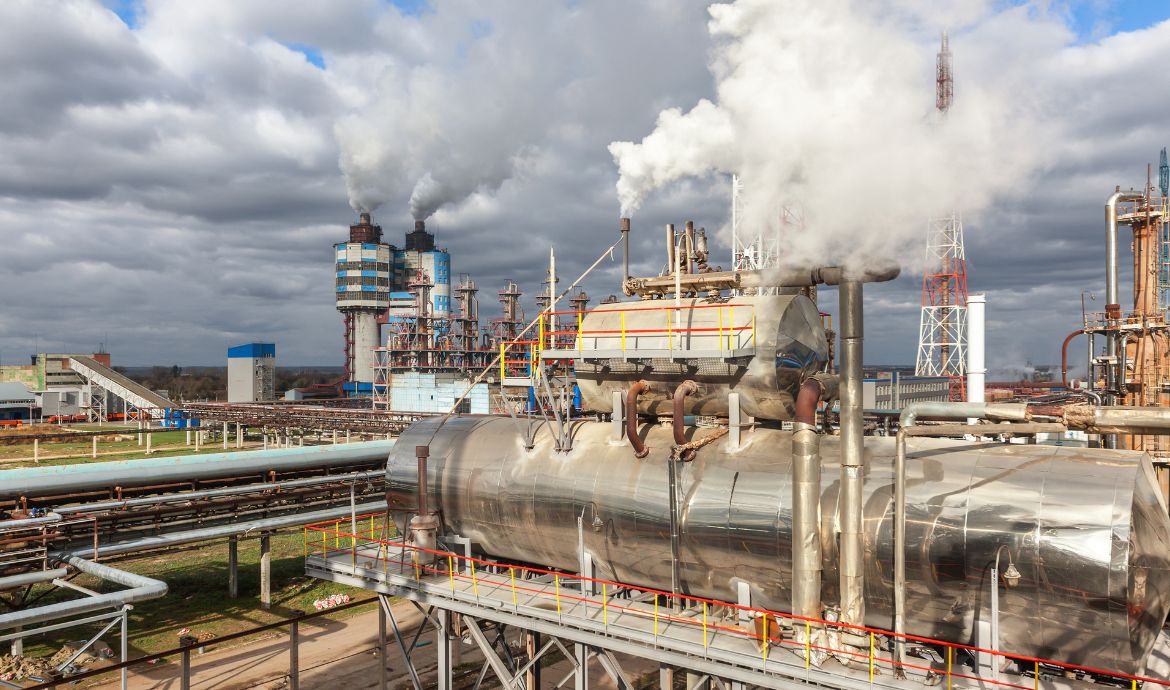
CATEGORY: LDPE Plants
PRODUCTS: High-Pressure Sensors
DATE: February, 2022
Background
A leading engineering company specialising in the design, development, and fabrication of high-pressure components for LDPE (Low Density Polyethylene) plants faced unique challenges. The manufacturing processes they cater to typically operate at pressures up to 2000 bar, necessitating temperature sensors of exceptional precision and durability.
SOLUTION
The company required high-pressure temperature sensors that could reliably function at pressures around 2000 bar. These sensors play a critical role in monitoring and controlling various high-pressure components, such as piping, reactors, valves, and pumps. For the sensors to be deemed suitable, they must pass pressure tests of up to 4600 bar at room temperature.
Thermo Electric Instrumentation partnered with the engineering company to develop, test, and certify custom high-pressure temperature sensors. The collaborative process involved:
- Development: Custom-designed sensors were engineered to withstand extreme pressure conditions.
- Testing: Rigorous tests ensured that the sensors could handle pressures of up to 4600 bar at room temperature.
- Certification: Test results and certifications of sub-assemblies were submitted to the engineering firm for pre-approval.
- Manufacture: Upon receiving approval, full-scale manufacturing commenced.
Customised Services
Our customised services extended beyond product delivery; we offered post-installation support, ensuring that our high-pressure temperature sensors were seamlessly integrated into the customer's system and performed at optimal levels.
ENGINEERING EXCELLENCE
Our engineers hold relevant certifications and have undergone rigorous training to become specialists in high-pressure sensor technology. They work closely with research and development departments to ensure that the solutions we offer are not only state-of-the-art but also sustainable and future-proof
RESULTS
The outcome of our collaboration with the project team has been nothing short of transformative, yielding tangible improvements across various metrics and operational aspects. Below are some of the notable results:
Accurate Monitoring and Enhanced Safety
The integration of our high-quality, high-pressure sensors into the project significantly enhanced the monitoring capabilities of the system. Not only did this improve the safety of the operation by allowing for real-time adjustments, but it also increased the lifespan of critical components, thus reducing long-term maintenance costs.
Elevated Operational Efficiency
Our custom-designed sensors allowed for more accurate temperature and pressure readings. This, in turn, facilitated tighter control loops and contributed to more efficient operational sequences. The result was a marked improvement in the overall process efficiency, reducing resource consumption and minimising waste.